views
Imagine you’re running a construction site, an oil rig, or a chemical plant. Every day, your team faces hazards that could turn a routine shift into a headline-grabbing disaster. Forklifts whizzing by, heavy machinery humming, or volatile substances just a spark away from trouble—it’s enough to keep anyone up at night. Now, add the pressure of regulations, insurance demands, and the very real need to keep your people safe. Overwhelmed yet? That’s where ISO 45001 comes in, like a trusty hard hat for your organization’s safety management. It’s not just a standard; it’s a game plan for protecting lives, saving money, and sleeping better.
If you’re in a high-risk industry—think construction, manufacturing, energy, or mining—ISO 45001 isn’t optional. It’s essential. This article will walk you through what ISO 45001 is, why it matters, and how its requirements can transform your workplace from a liability minefield into a model of safety and efficiency. Let’s get started, with a few real-world stories and a touch of grit to keep it real.
What Is ISO 45001, and Why Should You Care?
ISO 45001 is the global standard for occupational health and safety management systems (OHSMS). It’s a framework designed to help organizations prevent workplace injuries, illnesses, and fatalities. Think of it as a blueprint for building a culture where safety isn’t just a poster on the wall but a way of life. From identifying hazards to training workers to handling emergencies, ISO 45001 covers it all.
The Core Requirements: What Does ISO 45001 Ask of You?
Let’s break down ISO 45001’s requirements. Don’t worry—this isn’t a dry manual. Picture it like a recipe for a safer workplace, with a few key ingredients you’ll need to mix just right.
-
Leadership Commitment: Top management must lead the charge. This means setting safety policies, allocating resources, and walking the talk. No delegating to the intern—this is C-suite territory.
-
Worker Participation: Employees at all levels need a voice. From the welder on the factory floor to the site supervisor, everyone helps identify risks and suggest fixes. It’s teamwork, not top-down.
-
Hazard Identification and Risk Assessment: You’ll map out every danger—slippery floors, faulty equipment, toxic fumes—and figure out how to control them. Think of it as playing whack-a-mole with risks.
-
Legal Compliance: Stay on the right side of OSHA, EPA, or local regulations. ISO 45001 ensures you know the rules and follow them.
-
Training and Competence: Equip your team with the skills to work safely. This could mean toolbox talks, certifications, or drills for emergencies.
-
Incident Investigation: When something goes wrong, dig into why. A near-miss with a crane? A chemical spill? Investigate, learn, and prevent it from happening again.
-
Continuous Improvement: Safety isn’t a one-and-done deal. Regular audits and reviews keep your system sharp.
Sounds like a lot, right? It is, but it’s manageable. ISO 45001 is flexible—you tailor it to your industry, whether you’re running a refinery or a shipyard. The goal is progress, not perfection.
Why High-Risk Industries Can’t Afford to Skip This
You know what’s wild? Some companies still treat safety as an afterthought. I heard about a mining firm—let’s call them RockSolid Inc.—that ignored safety protocols to cut costs. One day, a conveyor belt malfunctioned, injuring three workers and halting operations for weeks. The fallout? Lawsuits, fines, and a PR disaster that tanked their reputation. Total cost: $12 million. A year later, they adopted ISO 45001, revamped their safety program, and haven’t had a major incident since. Coincidence? I think not.
The Emotional Win: Peace of Mind in a High-Stakes World
Let’s get real for a second. Running a high-risk operation is stressful. You’re not just managing budgets or schedules; you’re responsible for lives. One mistake—a loose scaffold, an untrained operator—could change everything. ISO 45001 takes some of that weight off your shoulders. It gives you a system to lean on, so you’re not reinventing the wheel every time a new hazard pops up.
There’s also a quiet pride in getting it right. Imagine walking through your site, knowing your safety protocols are airtight. Or getting a nod from an auditor because your records are spotless. That’s the kind of confidence ISO 45001 builds. And when your team sees you prioritizing their well-being? That’s loyalty money can’t buy.
A Real-World Example: How ISO 45001 Saved a Factory
Let me tell you about a chemical plant I came across (details tweaked for anonymity). They had a history of minor accidents—spills, burns, nothing fatal but enough to raise eyebrows. Regulators were circling, and morale was low. Then, their safety manager pushed for ISO 45001 certification. It wasn’t easy. They had to overhaul training, document every process, and get buy-in from skeptical workers.
Six months later, the results were staggering. Incidents dropped by 60%. Insurance premiums fell. Workers started reporting hazards proactively, knowing their input mattered. The plant even landed a major contract because the client required ISO 45001 certification. The safety manager told me, “It’s like we went from surviving to thriving.” That’s the power of a system done right.
The Implementation Process: No Need to Panic
Okay, so you’re sold on ISO 45001. But how do you actually make it happen? Here’s the thing—it’s a journey, not a sprint. Most organizations take 6-12 months to get certified, depending on their size and complexity. Here’s a quick roadmap:
-
Gap Analysis: Compare your current safety practices to ISO 45001 requirements. Where are the holes?
-
Build Your OHSMS: Develop policies, procedures, and controls. Use tools like Safesite or iAuditor to streamline documentation.
-
Train Your Team: From executives to frontline workers, everyone needs to know their role. Providers like BSI or TÜV SÜD offer ISO 45001 training.
-
Run Internal Audits: Test your system. Fix what’s broken.
-
Get Certified: Hire an accredited body (e.g., DNV, SGS) to audit your OHSMS. Pass, and you’re certified.
Sounds daunting? It’s not. Consultants can guide you, and software like Intelex or Cority can simplify the process. Plus, the payoff—fewer accidents, lower costs, happier workers—is worth every ounce of effort.
The Business Case: Safety Pays Off
Let’s talk dollars and cents. Implementing ISO 45001 isn’t cheap—expect to spend $10,000-$50,000 on training, consultants, and audits, depending on your operation. But the return on investment is undeniable. A 2023 study by the British Safety Council found that ISO 45001-certified companies saw a 20% reduction in downtime and a 15% boost in productivity. Insurance providers often offer discounts for certified firms, and clients are more likely to trust you with their business.
Then there’s the legal angle. Non-compliance with safety regulations can lead to fines, shutdowns, or worse. ISO 45001 keeps you ahead of the curve, so you’re not sweating bullets during an OSHA inspection.
Challenges to Watch For (Because It’s Not All Smooth Sailing)
Let’s keep it honest. Adopting ISO 45001 can feel like herding cats. Workers might resist new processes, especially if they’re used to “the old way.” Management might balk at the upfront costs. And the paperwork? It’s no joke—ISO 45001 loves its documentation.
But here’s the flip side: these challenges are surmountable. Clear communication, phased implementation, and a bit of patience go a long way. Start small—focus on one site or department—then scale up. And don’t skimp on training; it’s the glue that holds the system together.
Your Next Steps: Time to Act
Ready to make ISO 45001 your secret weapon? Here’s how to kick things off:
-
Learn the Standard: Grab a copy of ISO 45001 (available from ISO.org) and skim the basics.
-
Assess Your Needs: Conduct a gap analysis or hire a consultant to do it.
-
Rally the Team: Get buy-in from leadership and workers. Share success stories like the chemical plant’s.
-
Find a Partner: Choose a certification body and training provider you trust.
-
Take the Plunge: Commit to the process. It’s a marathon, but the finish line is worth it.
Still on the fence? Ask yourself this: can you afford another accident, another fine, another sleepless night? ISO 45001 isn’t just a standard—it’s a lifeline for high-risk industries.
The Bottom Line: Safety Is Your Legacy
You know what’s amazing? The impact you can have. ISO 45001 isn’t just about checking boxes or dodging fines. It’s about creating a workplace where people thrive, not just survive. It’s about knowing you’ve done everything in your power to keep your team safe. In high-risk industries, that’s not just a job well done—it’s a legacy.
So, what’s holding you back? A safer, stronger, more successful operation is within reach. Grab it.
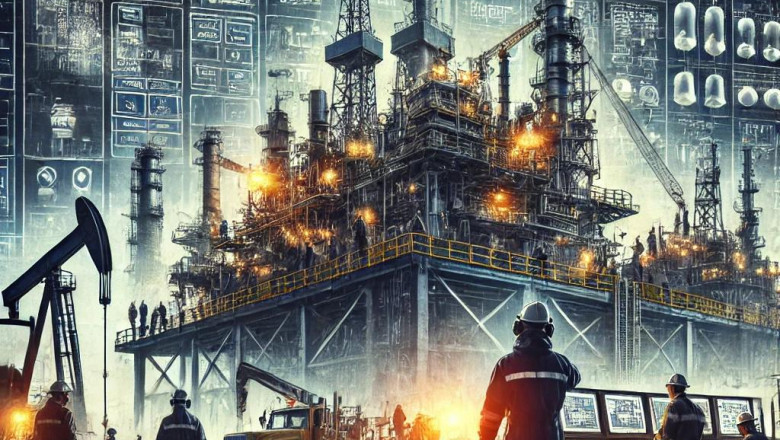

Comments
0 comment